
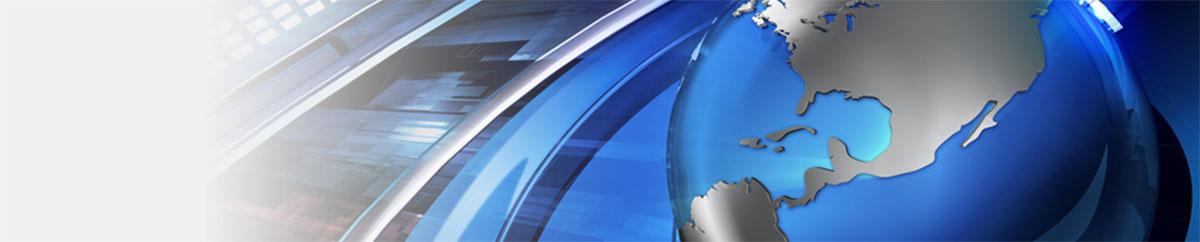
热门文章
高温合金的钻孔加工
高温合金分为铁基高温合金、镍基高温合金和钴基高温合金。是在760~1 500℃、一定应力条件下、长期工作的高温金属材料。具有优异的高温强度、良好的抗氧化和抗热腐蚀性能、良好的抗疲劳强度及断裂韧性等综合机械性能。广泛用于航天、航空、各种热处理设备。随着冶金技术的日益发展,高温合金的综合性能得以进一步提升,使得这种金属材料的加工难度不断增加。
1.高温合金的机械特性
高温合金的晶格组织细密,并含有许多高熔点合金元素 Fe、Ti、Cr、Ni、V、W和Mo等,这些合金元素与其他合金元素构成纯度高、组织致密的奥氏体合金。而且有的元素与非金属元素C、B、N等构成硬度高、比重小、熔点高的金属与非金属化合物。使切削加工性能变差。相对45钢的切削性能,高温合金的切削性能只有其5%~20%。高温合金与常用、金属机械属性对比矢量如图1所示。各类高温合金的材料特点相比如附表所示。
综合高温合金的切削加工特点如下:
(1)切削力大:高温合金的塑性好、强度高。在较高温度时,仍保持高强度。加工时所需切削力是普通合金钢材料的2~5倍。
(2)切削热量高:高温合金的导热系数小,加工时热量集中在切削区,不易扩散。致使切削刀具迅速磨损。
(3)切削表面硬化严重:高温合金的硬度不高,但塑性好。加工时切削区的晶格扭曲严重,冷作硬化现象高。已加工表面硬度比基体硬度高50%~99%。
(4)刀具磨损快,使用效率低:高温合金中含有大量的硬度高、比重小、熔点高的金属间化合物及非金属化合物,构成硬质点。使刀具机械磨损加剧。由于切削力大、切削温度高。在高温高压下,刀具与被切削材料极易产生黏接而造成黏接磨损。此外,在高温下切削,材料与刀具间的金属扩散现象加大,产生扩散磨损。极端情况下,一些普通材料的刀具(如高速钢类刀具),甚至无法完整切削高温合金。
(5)零件加工精度难以保证:由于前述几项原因,高温合金的表面加工完整性较难保证,精加工时常常在粗加工时产生的冷作硬化层中进行,有些刀具材料无法完成一个加工面的完整切削。特别是孔加工时的铰削加工,在加工时刀具本身对材料有挤压作用,极易发生黏刀、产生积屑瘤、刀具崩刃等现象。最终破坏加工表面。
2.加工高温合金的刀具材料选择
由于高温合金材料的难加工特性,使得选择适当的刀具材料来加工高温合金,至关重要。刀具材料的不同对高温合金的加工效率、表面加工质量有着明显效果。理论上加工高温合金首选陶瓷刀具,其次带涂层硬质合金刀具,再次无涂层硬质合金刀具,最次采用高速钢刀具。而各种刀具材料的选择要根据零件的加工要求、加工方式、工艺条件、加工环境、经济性等多项条件来决定。各种刀具材料的高温硬度与韧性的关系如图2所示。
由图2可知,金刚石、立方氮化硼、陶瓷类刀具硬度高,但韧性稍差。加工时易出现崩刃现象。可在连续无间断切削、开放式加工条件下优先选用。如外圆或端面的精加工车削。金属陶瓷、涂层硬质合金、细颗粒硬质合金(带涂层)、细颗粒硬质合金、无涂层硬质合金类硬度较高、韧性较好,适合在多种情况下加工高温合金。而高速钢及涂层高速钢韧性最好,但硬度最低。适合制作形状复杂的成型刀具。
3.加工高温合金刀具的几何角度选择
在相同的加工、冷却条件下刀具的几何角度不同。对切削加工的结果有着深远的影响。实验数据表明,在切削区域,切削过程中所产生的切削热约64%由切屑带走,18%导入工件,12%导入刀具,8%由周围介质(如切削液或空气)带走。因此,加快切屑的流速,使切削热快速流出切削区域,是降低刀具发生磨损的最有效措施。高温合金的导热性差,与刀具的粘接倾向大。材料中包含的金属间化合物及非金属化合物所形成的硬质点,加剧了刀具的磨损。同时也加大了切削热的产生。综合各项原因考虑,加工高温合金刀具应达到以下几点要求;
(1)在不影响刀具强度的情况下,尽量加大刀具前角γo。使切屑尽快流出切削区域,将热量尽快带离切削区域扩散。使切削区域温升降低,以减少刀具磨损发生。一般情况下γo≈10°不采用负倒棱。
(2)尽可能的减小刀具后角αf。后角的减小,使刀具的强度加大、刀具楔角增大。增大了刀具散热能力、减小了刀具磨损发生。通常采用αf=6°~8°。因高温合金切削后的表面易反弹,与刀具后刀面产生强烈摩擦。产生高温,磨损刀具。宜在切削区外磨出第二后角,以减少摩擦生热。第二后角αfˊ=10°~15°。
(3)粗加工时刃倾角λS=-5°~-10°,精加工时刃倾角λS=0°~3°。
(4)刀尖圆弧半径0.5~2mm,粗加工时取大值。
4.实践操作
生产工作中需要加工一种进口高温合金,牌号Inconel718。对应国家标准材料为GH4169。是一种镍基高温合金。工艺要求材料淬火处理,淬火后38~42HRC。需在工件上钻6个φ12.7mm孔,孔深40mm。由于批量小、工期紧。刀具采购周期长等条件限制,只能用W18Cr4V的普通高速钢钻头加工。
首先采用标准麻花钻加工。加工时,减小钻头横刃宽度,以减小钻削时的轴向力。并采用自动进给、冲水冷却。转速n=63r/min(线速度v=2.5m/min)、进给量=0.08mm。钻削深度<5mm时,钻头已磨损严重,不能继续加工。采用转速n=90 r/min(线速度v=3.6 m/min)、进给量=0.12mm。钻削深度<5mm时,钻头已磨损严重,不能继续加工。两种钻头磨损的情况:转速n=63 r/min(线速度v=2.5m/min)时,钻尖磨损较严重。转速n=90 r/min(线速度v=3.6 m/min)时主要是钻头外刃锋角处磨损。
钻头的线速度是以钻头外径来计算的,钻头中心的线速度理论为v=0 m/min。钻头主切削刃各点的切削速度从钻心到钻头外刃逐渐加大。钻头中心附近处因线速度太低,钻头材料与工件材料发生摩擦挤刮,产生高温并且不能及时排开、冷却,造成钻头中心迅速升温、磨损。钻头锋角的线速度最高,当线速度增高时,外刃锋角快速升温,因强度不足产生磨损。
以上的磨损产生都是线速度不当造成无法加工。但这两种线速度已经非常接近,不论调高或调低线速度,都会使另一种磨损情况加剧。所以,不能通过调整线速度来解决问题。当然,这是因为受刀具材料影响,如果采用硬质合金或高钒高速钢,这种情况就会得到改善。但是,目前只能用W18Cr4V的普通高速钢钻头来加工。
于是,尝试改变钻头的角度。针对钻头加工高温合金时的受力情况,合理采用刀具形状、刀具角度来解决问题。普通麻花钻头自身的结构决定了钻头的前角γo是由钻尖到外刃锋角逐渐加大的。钻尖处为0°甚至是负角度,锋角处最大,等于90°排屑槽的螺旋升角(普通麻花钻头的螺旋升角是60°,即90°-60°=30°),锋角处前角最大,楔角最小,刀具实体最尖锐,刀体强度最低。热量最不易散发;钻心处线速度最低,前角为负,受到的轴向抗力最大,钻尖与工件材料摩擦最严重。这是钻头在两种非常接近的线速度产生不同位置磨损的主要原因。也是我们无法加工的矛盾点。
锋角处线速度最高,温升最快。而且,锋角处刀体强度最低,极易发生各种磨损,使刀具失去锋利。因此,通过改变锋角前角γo的大小、改变锋角的形状等方法来强化刀具,使刀具减少磨损、保持锋利。是提高刀具使用寿命的有效手段。强化后的外刃锋角可以承受相对较高的线速度。
在同样转速下,钻头的顶角2φ越大,所受到的轴向抗力越大。产生的热量多积聚在最前端的钻尖处,使钻尖温升加剧、磨损迅速。所以,钻尖处宜采用较小顶角,以减小轴向抗力,降低温升。但钻尖处采用较小顶角时,钻尖的强度减弱。钻头磨损加剧。为了强化钻尖强度,需要选取钻芯较厚的钻头,并不再刃磨钻尖前角,保留钻头横刃宽度。使钻尖实体加大,强度提高。以减少钻尖磨损。
综合上述原因考虑,我们设置出图3的群钻,来加工这种淬火镍基高温合金。其中,2φ=160°~170°,2φ2=70°~80°,γ=10°,αf=6°~8°,Ψ=70°~75°,h=2mm,b=2~3mm,r=1.2~1.5mm,αf′=6°~8°。
使用这种钻头,采用转速n=90r/min(线速度v=3.6m/min)、进给量=0.08mm,刃磨一次可以钻深40mm。即可以完成一个孔的加工。完成了原本无法完成的任务。
这种钻头的钻尖处顶角(第一顶角2φ2=70°~80°)采用小后角αf=8°~10°,因此横刃斜角Ψ较大Ψ=70°~75°。横刃实际宽度b=2~3mm。同时,在主切削刃后大于约1mm处刃磨出第二后角αf′=10°~15°。这样,横刃就由一条直线变为近似S形的折线,从侧面看形成一个大角度的顶角2φ′=175°,使得钻尖得到近一步强化。第二顶角2φ=160°~170°承担了主要的轴向抗力。
将钻头的两个锋角倒圆,形成r=1.2~1.5mm的圆弧型锋角。并对两锋角的前角刃磨至γo=10°(仅锋角处2mm,其余各处前角γo不变),极大程度强化了锋角,降低了锋角的磨损发生。使钻头外刃锋角在转速n=90r/min(线速度v=3.6m/min)时钻头外刃锋角处不易磨损,可以正常加工。
同样,在第二顶角2φ的主切削刃后大于约1 mm处刃磨出第二后角αf′=10°~15°。以减少钻头与工件材料之间的摩擦。并将后刀面尾部约1/4处磨去。以增大钻头的容屑、容液空间。
5.结语
加工时,由于第一顶角小,轴向抗力大大减少。使得切入顺利,由于保留了钻头横刃,使刀尖强度增强不易磨损。第二顶角承担了主要的轴向抗力,但第二顶角的主切削刃偏离钻心,有一定的线速度。就有了切削力,不会有挤刮产生。切削升温就得到了控制。
相比标准麻花钻,这种高温合金群钻保留了横刃宽度,采用小顶角的方式有效解决了钻头中心线速度低,轴向抗力大,温升快、钻尖易磨损的问题。圆弧形的外刃锋角,并配合10°的前角γo,使线速度高的部分得以最大的强化。钻头的使用寿命得到成倍的提高。
加工实践证明,钻削加工过程中,钻头与被加工材料之间的摩擦使钻头与被加工材料快速升温。因此,采用油冷却比采用水冷却效果要好。油的冷却效果比水差,但温的润滑作用使切削升温得到抑制。
该文章转自于:机工刀具世界 https://mp.weixin.qq.com/s/7YdM2d8A4M-XFXaFDE1jdA