
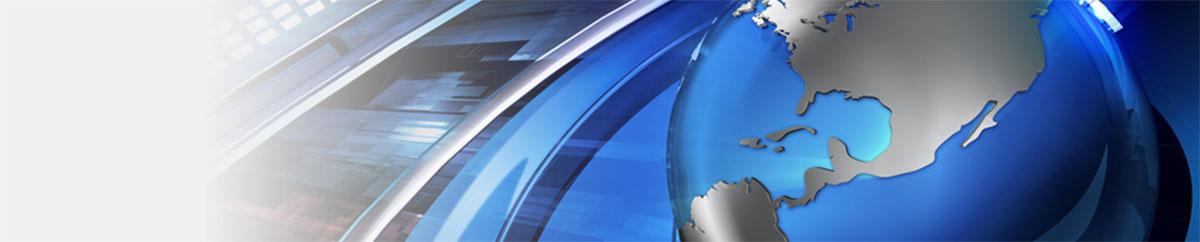
热门文章
激光焊接技术在航空制造中的应用
随着长寿命、高可靠性、低成本、高性能的设计及制造要求,越来越多的新型高性能材料、复杂结构在飞机及航空发动机设计中被广泛应用,如整体壁板、整体叶盘/叶环、空心叶片、单晶/定向凝固叶片、粉末合金及复合材料构件等。新型高性能材料、复杂结构的扩大使用,在提高装备性能的同时,也对包括焊接技术在内的航空制造及修理技术提出了更高的要求。
激光焊接具有能量密度高、热输入量低、结构变形小、无需真空环境、高质量、高精度、高效率等技术优势,在各类金属材料熔化焊接方法中独占鳌头;结合工业机器人、视觉传感跟踪系统、自动送丝(送粉)系统(见图1),易于实现集成化、自动化、柔性化、批量化制造,在全球制造产业中占据越来越高的地位。近年来,随着高功率激光器的不断发展,激光束流品质的不断提高,激光焊接技术实现了由传导焊向深熔焊的根本性转变,应用范围进一步扩大,在航空制造及修理中重要性也不断提高。
图1 搭载机器人的激光填丝焊接系统
1. 激光焊接在飞机制造及修理中的应用
(1)激光焊接在飞机制造中的应用 在飞机制造领域中,激光焊接技术主要应用于飞机大蒙皮的拼接以及蒙皮与长桁的焊接,机身附件的装配中也大量使用了激光束焊接技术,如腹鳍和襟翼的翼盒。近年来,激光焊接技术也多用于薄壁零件制造,如进气道、波纹管等。
早在20世纪70年代初,美国已利用15kW的CO2激光器针对飞机制造业中的各种材料、零部件,进行了焊接试验及评估工艺的标准化。美国爱迪生焊接研究所与海军焊接中心联合开展了战机装备激光焊接技术研究。意大利于20世纪70年代末从美国引进了15kW的CO2 激光器,随后欧盟对航空发动机中的各种容器及轻量级结构立项,开展了长达8年的激光焊接应用研究,材料涉及钛合金、镍基、铁基高温合金等。英国焊接研究所(TWI)成功实现了铝合金加筋壁板双光束YAG激光填丝焊接,焊接质量良好,焊接变形小于TIG焊。德国宇航公司(MBB)将激光焊接用于飞机机身、机翼与内隔板和加强筋的全部连接,取代了原有的铆接工艺,被德国宇航界称为航空制造业中的一大技术革命。
2002年前后,空客公司采用双光束双侧同步激光焊接工艺(见图2),将A318铝合金飞机机身两块下壁板的蒙皮与桁条焊接成整体机身壁板,减轻飞机机身的重量近20%,提高强度近20%,后续推广应用于A380、A340、A350等多个机型的机身整体壁板制造,以及A380的舱壁门筋板以及无人驾驶飞机结构,在A350上的焊缝总长度更是达到1000m。
图2 双激光束双侧同步激光焊接
我国激光焊接技术研究起步于20世纪80年代,经过多年努力,已成功实现了汽车制造拼焊、管道焊接应用。随着铝合金、钛合金激光焊接工艺基础研究的深度、广度不断增大,已实现了部分飞机构件的激光焊接应用。
自20世纪90年代后期开始,中航工业北京航空制造工程研究所就已经开展了飞机构件激光焊接技工艺研究。2003年,在国内率先将激光焊技术应用于飞机钛合金壁板类关键构件的焊接,同时在激光填丝焊接、激光电弧复合焊接、激光双光点焊接、T形接头激光双光束双侧同步焊接技术等新工艺方面也进行了大量研究。2014年左右,在国产大型客机设计方案中,前机身、中后机身的部分铝锂合金下壁板拟采用激光焊接方案,中国商飞公司牵头开展了工艺稳定性分析、变形控制,以及缺陷检测与控制等相关研究工作,初步实现了试验件级构件的激光焊接(见图3)。
图3 铝锂合金激光焊接壁板试验件
(2)激光焊接在飞机修理中的应用 激光焊接技术具有焊接速度快、施工较铆接简单的特点,是代替铆接工艺的理想技术,在飞机结构修理领域具有较大的应用优势。国内已就激光焊接技术修理飞机构件开展了一些研究,并已实现了部分构件的修理应用。国内某飞机修理工厂已将激光焊接技术应用于飞机钛合金机尾罩的损伤修理,并制定了钛合金结构激光焊接修理工艺规范。2012年左右,空军第一研究院采用机器人柔性激光切割/焊接系统,完成了某型飞机机翼钛合金蒙皮下表面损伤部位的切割、焊接一体化修复应用研究,修复后表面光滑,结构性能完全恢复,可长期可靠工作,满足了使用需求。
2. 激光焊接在发动机制造及修理中的应用
(1)激光焊接在发动机制造中的应用 激光焊接技术以其优异的热源性能、极佳的变形控制优势及较广的材料焊接适应性,在航空发动机薄壁高精度构件焊接方面独具优势(见图4),在航空高温合金、钛合金、钛铝金属间化合物等新型材料焊接方面有较大的发展前景。国外极为重视航空构件激光焊接技术的研发与应用,欧盟第六框架研究项目AROSATEC针对压气机定子与叶栅、高压和低压叶片出口与盖板连接,以及涡轮机匣开展了激光焊接技术研究。
图4 航空结构件的激光焊接
美国普惠公司完成涡轮叶片所需部件的自动激光焊接,如JT9D和FLO的二级涡轮转子叶片以及V2500、F100-PW-220、PW2037、PW4000等发动机的涡轮叶片、导向叶片、机匣及燃烧室等。美国GE公司也已成功完成了发动机导向叶片组件的激光焊接,有效地解决了镍基合金零件激光焊接变形与裂纹等问题,并用6kW的CO2 激光设备焊接了喷气发动机燃烧室衬套。英国R&R公司用固体激光器与机器人组合完成钛合金和高温合金的自动化焊接,保证了焊缝和焊接过程的一致性,减少了焊接变形,接头残余应力低,大大减少了校形工作量。日本JAEC的相关公司采用6kW的CO2激光设备完成了V2500发动机的风扇机匣前后段焊接。
早在20世纪90年代末期,某公司就与西北工业大学联合攻关,开展了Inconel625高温合金航空发动机前、后冷气导管的激光焊接工艺研究,采用了CO2激光焊接设备,开发了从焊前清洗、装配焊接到焊后处理等全套焊接工艺,满足了使用需求。北京航空制造工程研究所已将激光焊接技术应用于发动机钛合金承力构件制造,并采用激光焊接技术替代板扩散连接技术,在国内率先开展了钛合金超塑成形/激光焊的多层结构制造工艺研究。波音公司和华盛顿州立大学联合也开发了超塑成形和激光焊接的组合工艺,通过激光焊接方法可以更加灵活的构造芯板图案,大大提高生产效率、降低成本。
(2)激光焊接在发动机修理中的应用 发动机部件主要损伤形式有外物打伤、磨损、裂纹、烧蚀和加工缺陷等,部件材料、损伤部位、损伤形式的多样性,决定了损伤后焊接修复的复杂性。激光焊接修复技术利于近净成形,减少裂纹产生,大量应用于航空发动机零部件修理(见图5、图6)。
图5 激光堆焊修复叶片叶冠损伤部位
图6 激光焊接补片修理整体盘叶片
美国霍尼韦尔公司已经成功将激光焊接技术应用于Avro RJ支线喷气系列飞机发动机LF507的叶片修理。加拿大Liburdi集团公司采用自动送丝激光焊接设备进行叶片修理,已实现了RB211发动机高、中、低压涡轮叶片修理(见图7),并于2001年获得R&R公司授权专门从事RB211发动机叶片和其他部件的激光焊接修复。德国MTU公司开发了可用于风扇整体叶盘的叶片损伤修复的激光焊接技术,形成了焊接、机械加工、精密抛光和无损检测修理规范。
图7 自动送丝激光焊修理涡轮叶片
激光低热输入精密金属沉积工艺是H&R公司的专利技术,与激光填丝焊接类似,主要是利用激光熔化金属扁丝进行一层一层地堆积,不同的是,这种技术无需待修理件上建立熔池。美国海军和空军已将该技术成功地应用于受损整体叶盘修理,使修理时间缩短、精度提高、费用减少、寿命延长,并在T700发动机压气机第1级整体叶盘上得到验证。在此基础上,H&R公司针对普惠公司F135发动机修理,完成了相关的高循环疲劳试验和评估,达到与T700发动机压气机整体叶盘相同的修理水平。
国内在激光增材修复技术方面开展了较多的研究,已完成了多种结构、材料发动机构件的修理验证,但在激光焊接修理应用研究相对较少。中科院金属所采用激光显微焊进行原位无损修复,该技术具有可获得内应力最小、空间界面结合最好、缺陷立体修复区最小的优点,已成功应用于我国研制的某机空心导向叶片的铸造工艺孔修复,以及低压涡轮1、2级三联体无余量精铸导向器叶片大小安装板上的疏松、缩孔与裂纹等缺陷的修理,通过了装机台架试车考核。沈阳发动机设计研究所和沈阳黎明公司联合开展了某型发动机高压涡轮工作叶片叶尖裂纹激光焊修理技术研究,通过了300h热冲击试验考核,符合大修叶片故检标准,满足了使用要求。沈阳黎明航空发动机公司针对发动机主机点火导线深度修理需求,开展了激光焊接修理工艺研究,先后完成6件试验件级修理验证,形成正式修理工艺,完成了两台点火导线修理应用,修理后的点火导线外观及各项电气性能均合格,并通过了试车。在修复某型发动机中介机匣时,对固连环形壳体与支撑板氩弧焊焊缝上的裂纹实施了激光补焊,焊缝成形良好,前后变形量符合要求。
3. 几点建议
(1)加快关键焊接设备自主研发 学习国外先进激光器研制经验,引进、消化、吸收、再创新,加快适用于航空装备产品特点的高功率、高光束质量激光器,以及自动送丝、视觉跟踪、在线检测等配套系统的自主研发。
(2)增大激光焊接技术研究深度 建立稳固的校企、研究所合作研发关系,以制造企业应用需求为导向,增大激光焊接技术基础研究深度,如气孔、裂纹等缺陷形成机制及抑制、接头表面完整性及可靠性评估等,开发适用于高温、复杂应力等苛刻环境服役需求的修理用焊接材料,满足高质量、高精度焊接修理要求的工艺配套技术、修理前后处理技术。
(3)重视新型材料焊接工艺开发 积极开展高强高温钛合金、新型高温合金、钛铝系金属间化合物、单晶/定向/粉末高温合金等新型航空材料的激光焊接工艺开发,形成涵盖材料焊接性、工艺、接头组织及性能的工艺数据储备,建立相应的激光焊接工艺流程。
(4)加快新型焊接技术应用研究 针对航空产品材料及设计结构特点,加快适用于航空制造及修理需求的新型激光焊接方法应用研究,如激光填丝自动焊、长焦距激光焊、激光复合焊及双光束(填丝)焊等。
(5)扩宽激光焊接工艺应用广度 借鉴国外航空制造成功经验,建立设计-材料-制造的一体化研发模式,推进激光焊接技术在航空飞机及发动机典型构件上的工程应用,如飞机整体壁板、腹鳍和襟翼等,发动机的各种薄壁机匣、燃烧室部件、叶片等复杂、精密构件,以及加力筒体、扩散器等简单焊接结构件等。
(6)建立完善的工艺质量标准体系 结合新材料、新结构、新方法及新产品研制及应用进展,逐步建立和完善我国激光焊接工艺、质量标准体系,同时建立并不断完善焊接工艺数据库。
(7)加快自动化、智能化进程 结合工业机器人系统、自动送丝系统、视觉传感跟踪系统、焊接质量在线检测、评估及实时控制系统,助推航空产品自动化、智能化制造实现,提升激光焊接工艺自适应控制能力及生产效率。
该文章转自于:焊接切割联盟 https://mp.weixin.qq.com/s/kGMaqBodNMvVooYb1g1Srg
上一篇:铝合金典型焊接缺陷与返修诀窍!
下一篇:合金元素在钢中的作用