
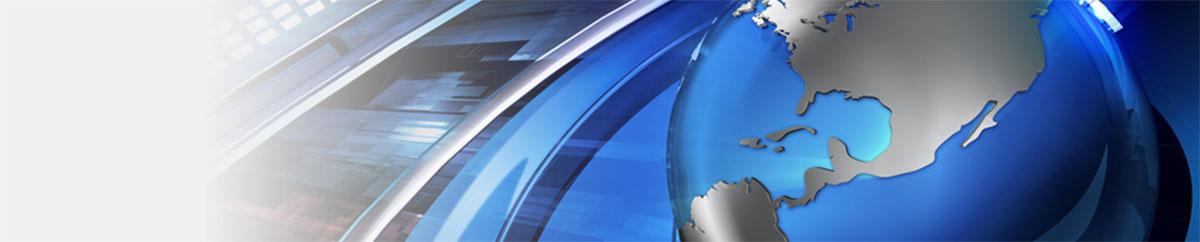
热门文章
【焊接工程师】全面详解铝及铝合金焊接工艺规程
本规程规定了铝及铝合金焊接的基本要求,适用于铝及的手工钨极氩弧焊或气焊或熔化极氩弧焊等焊接的铝及铝合金制单层容器、衬铝容器的铝焊接工艺。
一、焊接用材料:
1.焊接用氩气纯度≥99.99%,露点≤-55℃,并应符合GB/T4842或GB10624的规定。当瓶装氩气的压力≤0.5Mpa时不宜使用。(氩气内含氮量≥0.04%,否则焊缝表面上会产生淡黄色或草绿色的氮化镁及气孔;含氧量≥0.03%,否则熔池表面上可发现密集的黑点、电弧不稳和飞溅较大;含水量≥0.07%,熔池将沸腾并焊缝内产生气孔)。
2.手工钨极氩弧焊电极采用铈钨电极。电极直径应根据焊接电流大小来选择(使用时一般比焊接电流所要求的规格大一号的钨极),电极端部应为半球形(制作半球形方法:用比焊接电流所要求的规格大一号的钨极,将端部磨成锥形,垂直夹持电极,用比所用钨极要求的电流大20~30A的电流在试板上起弧并维持几秒钟,钨极端头即呈半球形。如果钨极被铝污染,则必须重新打磨或更换钨极;轻微污染时,可增大电流使电弧在试板燃烧一会,即能烧掉污染物):
铈钨电极直径mm | 2 | 2.5 | 3.2 | 4.0 | 5.0 |
(正接时)焊接电流A | 100~200 | 170~250 | 200~300 | 350~480 | 500~675 |
(反接时)焊接电流A | 15~25 | 17~30 | 20~35 | 35~50 | 50~70 |
(交流时)焊接电流A | 85~160 | 120~210 | 150~250 | 240~350 | 330~460 |
3.用MIG焊铝合金时,由于铝焊丝比较软,为避免咬伤焊丝,送丝轮不允许用带齿轮的送丝轮,不宜用推丝式;送丝软管不准用弹簧管而是用聚四氟乙烯或尼龙制品,不然由于磨削而污染或堵塞软管。MIG通常用直流反极性。
4.焊剂主要作用是去除氧化膜和其它一些杂质,使用时可用无水酒精调成糊状或直接将焊剂粉放在坡口和两侧。当焊接角焊缝时应选用那些焊后容易清除熔渣的焊剂;铝镁合金用焊剂不宜含有钠的组成物。
5.不同牌号的铝材相焊时,当图纸和工艺都没有规定时,按耐腐蚀性能较好和强度级别较低的母材去选择焊丝材料。在焊接铝镁合金或铝锰合金等耐蚀铝合金时,宜采用含镁量或含锰时与母材相近或比母材稍高的焊丝。焊丝可从GB/T10585《铝及铝合金焊丝》选取,也可从GB/T3190《变形铝及铝合金化学成分》和GB/T3197《焊条用铝及铝合金线材》中选取。焊丝选用时可参考下面几个表(表3和表4摘自《焊接手册》):
表1 同牌号铝焊接用焊丝
同牌号母材牌号 | 焊 丝 | 同牌号母材牌号 | 焊 丝 |
1060 | SAL-3 | 5052 | SAlMg-1 |
1050A | SAL-3 | 5A02 | SAlMg-1 |
5A03 | SAlMg-2 | ||
1200 | SAL-1 | 5083 | SAlMg-3 |
3003 | SAlMn | 5A05 | SAlMg-5 |
3004 | SAlMn | 6061 | SAlMg-1 SAlMg-5 SAlSi-1 |
表2 异种铝焊丝焊接用焊丝
异种母材 | 焊 丝 |
纯铝+铝锰合金 | SAlMn |
纯铝、铝锰合金+5052、5A02 | SAlMg-1、SAlMg-5 |
纯铝、铝锰合金+5A03 | SAlMg-2 |
纯铝、铝锰合金+5083、5086 | SAlMg-3 |
纯铝、铝锰合金+5A06、5A05 | SAlMg-5 |
表3 针对不同的材料和性能要求选择焊丝
材 料 | 按不同性能要求推荐的焊丝 | ||||
要求高强度 | 要求高延性 | 要求焊后阳极化后颜色匹配 | 要求高强度 | 要求焊接时裂纹倾向低 | |
1100 | SAlSi-1 | SAl-1 | SAl-1 | SAl-1 | SAlSi-1 |
2A16 | SAlCu | SAlCu | SAlCu | SAlCu | SAlCu |
3A21 | SAlMn | SAl-1 | SAl-1 | SAl-1 | SAlSi-1 |
5A02 | SAlMg-5 | SAlMg-5 | SAlMg-5 | SAlMg-5 | SAlMg-5 |
5A05 | LF14 | LF14 | SAlMg-5 | SAlMg-5 | LF14 |
5083 | ER5183 | ER5356 | ER5356 | ER5356 | ER5183 |
5086 | ER5356 | ER5356 | ER5356 | ER5356 | ER5356 |
6A02 | SAlMg-5 | SAlMg-5 | SAlMg-5 | SAlSi-1 | SAlSi-1 |
6063 | ER5356 | ER5356 | ER5356 | SAlSi-1 | SAlSi-1 |
7005 | ER5356 | ER5356 | ER5356 | ER5356 | X5180 |
7039 | ER5356 | ER5356 | ER5356 | ER5356 | X5180 |
注:ER铝焊丝为美国标准ANSI/AWS A5.10。
表4 一般用途焊接时焊丝选用
母材之一 母材之二 | 7005 | 6A02 6061 6063 | 5083 5086 | 5A05 5A06 | 5A03 | 5A02 | 3A21 3003 | 2A16 2B16 | 2A12 2A14 | 1070 1060 1050 |
与母材配用的焊丝 | ||||||||||
1070 1060 1050 | SAlMg-5 | SAlSi-1 | ER5356 | SAlMg-5 LF14 | SAlMg-5 | SAlMg-5 | SAlMn | - | - | SAl-1 SAl-2 SAl-3 |
2A12 2A14 | - | - | - | - | - | - | - | - | SAlSi-1 BJ-380A | |
2A16 2B16 | - | - | - | - | - | - | - | SAlCu | ||
3A21 3003 | SAlMg-5 | SAlSi-1 | SAlMg-5 | SAlMg-5 | SAlMg-5 | SAlSi-1 | SAlMn SAlMg-3 | |||
5A02 | SAlMg-5 | SAlMg-5 | SAlMg-5 | SAlMg-5 LF14 | SAlMg-5 | SAlMg-5 | ||||
5A03 | SAlMg-5 | SAlMg-5 | SAlMg-5 | SAlMg-5 LF14 | SAlMg-5 | |||||
5A05 5A06 | SAlMg-5 LF14 | SAlMg-5 | SAlMg-5 LF14 | SAlMg-5 LF14 | ||||||
5083 5086 | SAlMg-5 | SAlMg-5 | SAlMg-5 | |||||||
6A02 6061 6063 | SAlMg-5 SAlSi-1 | SAlSi-1 | ||||||||
7005 | X5180 |
二、施焊焊工:
应按《铝容器焊工考试规则》附录A的规定考试合格。
三、焊前准备:
1.铝材坡口加工应采用机械方法(含剪切),如采用等离子火焰方法加工应从变色部分机械加工去掉不少于3mm,加工后的坡口表面应平整、光滑,不得有裂纹、分层、夹杂、毛刺、飞边和氧化色。坡口表面应呈银白色的金属光泽;必要时对坡口及两侧不少于50 mm范围内进行100%PT。
2.焊丝、坡口表面及其两侧不少于50 mm范围内必须进行表面清理(包括去表面氧化膜、鳞片、污染和不合格的氧化色)。打磨可用φ0.15~0.2不锈钢丝盘刷、金属磨头(即电动铣刀)、手工盘铣机、锉刀(应是铝专用弧形锉刀)、刮刀和丙酮(沾丙酮的白布应干净,不要使用棉布或棉纱,以避免擦拭时带出毛绒),但应注意这些工具在使用前应被清理干净,清理时也应注意不要把氧化膜以压入母材内,因此清理时不要太用力;但不准用砂轮或普通砂纸打磨,因为铝材很软而导致砂粒留在铝材里,焊后就易产生气孔和夹渣等缺陷。
3.对于外委热加工的部件,如封头等,原则上在进厂后应对铝材表面进行100%PT,必要时对不能确定的部位进行RT。
4.焊丝表面可用不锈钢丝刷或干净的油砂纸擦洗;对表面氧化皮较厚的焊丝在焊前打磨后还需要化学清理。化学清理:用70℃、5%~10%的NaOH溶液浸泡0.5~3min左右后用清水冲洗,接着用15%左右的HNO3溶液在常温下浸泡约1~2min后用温水冲洗,再用手持式吹风机(不能用空气压缩机,因为空气中有水和油)吹干再放入烘箱中100℃烘干即可使用。对铝材也可参考此法。
5.清理干净的焊丝和焊件应保持清洁和干燥,不得用手触摸和口吹焊接部位,焊工一般戴白色的焊工手套,不要因为怕麻烦而戴脏手套;焊前严禁污染,否则应重新进行清理,局部污染可局部重新清理;最好用白纸覆盖在坡口用两侧。一般机械清理后应立即焊接,如清理后4h之内未焊,焊前就应重新清理。
6.焊件装配应准确,如果装配不良时,应考虑换部件,而不得强行组对,以避免造成过大的应力。在正式焊接前应对坡口尺寸进行检查,合格后方可施焊。
7.定位焊选用的焊丝及采取的工艺措施与焊接工艺相同。
8.焊件组对时在应力集中处(如焊缝交叉处和工件上的转角处等)尽量避免进行定位焊,定位焊缝长度和间距可按下表:(mm)
母材厚度 | 定位焊间距 | 每段定位焊缝长度 |
<3 3~6 >6 接管或法兰 | 40~50 50~60 50~80 2~4点 | 4~6 5~10 10~12 每点3~8 |
9.定位焊缝不得有裂纹、气孔、夹渣等缺陷,否则必须清除重焊。重焊应在附近区域进行,而不要在原处点焊;对接焊缝间隙在工艺没规定时,可按2~4mm。
10.对于会熔入永久焊缝的定位焊缝必须保证焊透和清除其表面的氧化层(只允许银白色),并使焊缝两端平滑过渡以便于接弧,否则就应修整。在冷态零件上施焊时,电弧应在始焊稍作停留一下,待母材边缘开始熔化时,再及时加丝焊接,以保证始焊点焊透。
11.焊接纵缝时,必须在焊件两端放置引弧板和退弧板,引弧板和退弧板采用与被焊件相同牌号和厚度的铝材。焊接环缝时尽量避免产生弧坑。
12.焊接过程中定位焊点开裂,造成板边错位或间隙变化,应立即停止焊接,经修复后才能继续施焊。
13.在焊接过程中,应先钢丝刷清理上层焊缝表面的黑灰和氧化物。焊时注意处理火口,即收弧处。引弧可在离焊接始端10~20mm,再迅速回始端焊接,第一层采用直线焊接,为了获得良好的成形,其它层焊时可以横向摆动,并在两侧稍停一下,以便熔合。
14.铝焊接变形和焊时易产生塌陷,因此在焊前应有针对性地制作夹具和垫板。采用夹具时一般零件正反面都需要夹紧,并且夹具的刚性和夹紧力大小要适中,因为过小取不到控制变形作用,过大则焊缝拘束度太强易导致焊缝开裂,夹紧力按350Kg/100mm为宜。软性铝材夹具可为碳钢或不锈钢,可以减缓散热;强化铝材可用铝材制造夹具,这样可以加强散热。纵缝夹具可用琴键式,环缝可用液压胀形夹具。纵缝装配时可适当增大间隙,以便焊后有收缩余地;环缝(包括圆形凸缘、法兰等)则留些反向错边或扳边,因为焊后凸缘会塌陷变形。垫板材料一般为不锈钢或碳钢,对要求不高的铝材焊接可用石墨制作垫板。选择垫板材料还应考虑对焊缝冷却速度的影响。当铝板较厚或垫板装配间隙较大时,可用粘土泥封住间隙,焊后去掉即可。垫板尺寸可按下图:
材料及尺寸 | A | B | C |
不锈钢或碳钢 | |||
石 墨 |
四、焊接要求:
1.持证焊工应按焊接工艺文件和其它文件焊接。
2.在焊接环境出现下列情况之一时,应采取有效防护措施,否则不准施焊:
1) 焊接环境不清洁,有灰尘、烟雾;
2) 焊接环境风速大于或等于1.5m/s;
3) 焊接环境相对湿度大于80%;
4) 下雨、下雪的室外作业;
5) 焊接温度低于5℃;
3.铝材产品焊接设在专门的场地,场地应铺设橡胶或绒布;焊接时应远离通风口和门窗以避免影响气体保护效果。
4.用手工钨极氩弧焊焊接铝材一般都使用交流,以便产生阴极雾化的作用;熔化极氩弧焊则用直流反接。当由于设备所限采用直流焊接时,焊缝表面一般有一层氧化膜甚至是黑灰,这时可用钢丝刷或抹布擦去。对焊缝表面由于焊剂熔剂残留物或氧化而形成的白色膜可用钢丝刷或抹布醮热水擦去。
5.焊前预热:由于铝材导热性能很强,因此一般手工钨极氩弧焊焊接大于10mm厚度时,焊前都应预热,但不超过100℃,焊时层间温度也不超过100℃。可视具体情况用火焰或远红外线板进行加热。
6.在焊接过程中焊丝的填入点不应位于电弧正下方,而应位于熔池边部,距电弧中心线约0.5~1.0mm处,焊丝填入点不得高于熔池表面或在电弧下横向摆动,以避免影响母材熔化,破坏气体保护而使金属氧化;焊丝回撤时勿使焊丝未端露出气体保护区外,以免焊丝未端被氧化后再度送进时随之带入熔池。焊接时若钨极碰到焊缝金属应立即停止焊接,用金属磨头清除污染,并修磨钨极;无论焊前还是焊接过程中,都应先切除焊丝端部已氧化的部分再焊。
7. 一条焊缝应尽量一次焊完,不得已中途停焊后重新焊接时,应重叠10~20 mm。多层焊缝在进行下一道焊缝前,对前道焊缝进行表面颜色检查,只允许银白色;并彻底清除表面污染、夹渣等缺陷。弧坑应填满,接弧处应熔合焊透。一般熄弧采用堆高熄弧法:收弧时匀速抬高电弧,同时加速填充焊丝,直至电弧熄灭,使熄弧处焊缝局部凸出,必要时打磨超标的余高。在焊机上有衰减装置时,此熄弧方法效果更好。
8.A、B类接头焊缝的余高、余高差及宽度差下表 mm:
焊缝位置 | 焊缝余高 | 焊缝余高差 | 焊缝宽度差 | ||
钨极氩弧焊 | 熔化极氩弧焊 | 手工焊、半自动焊 | 自动焊、机械化焊 | ||
平焊 | 0~3 | 0~5 | 0~2 | 0~3 | 0~2 |
除平焊外的其他焊缝位置 | 0~4 | 0~5 | 0~3 | 0~3 | 0~2 |
9.接管与壳体的D类焊缝当壳体厚度≤12mm时,一般应将壳体扳边对接焊,扳边高度为25~30mm。
10.C、D类接头的焊缝厚度t,在图样上无其他规定时,应不小于组成角焊缝两边构件厚度δ1、δ2较小值的0.7倍,且不应小于3mm,在一般情况下不超过10 mm(按下图);在衬里或复合板复合采用盖板搭接角焊缝时,盖板厚度构成了角焊缝的一侧边长度L2一般较薄,使得焊脚长度受到侧边长度的限制,当L2≤4mm时,应要求t≥0.7 L2。
11.C、D类接头的焊缝与母材应呈圆滑过渡。
12.焊缝和热影响区表面应进行100%检查,不得有裂纹、未熔合、气孔、弧坑、夹渣和飞溅物等缺陷,焊缝外不应有打弧点。
13.铝材压力容器焊缝表面不应有咬边。常压容器焊缝表面的咬边深度不应大于0.5mm,咬边连续长度不应大于100mm,焊缝两侧咬边的总长度不应超过该焊缝长度的10%。
14.换热器换热管焊接顺序:管板组装(换热管预留长度应不少于4mm,以便后面的机加工);管端及管板清理;一端胀管;焊接一面管板;机加工未焊换热管管端;胀管;管端及管板清理;焊接未焊一面的换热管。焊接时第一层一般不加丝焊(第一层是否进行PT或气密性检测按规定),但其它层应加丝焊。
15.铝焊接应注意坡口钝边较大,一般为2~6mm。对有垫板的接头,钝边可适当减小。当铝板较薄时,对接焊都应考虑扳边对接焊,如当≤3mm考虑扳边和不加丝焊。铝焊接可采用双面同时焊,背面加丝或不加丝视具体情况而定。
五、焊缝返修:
1.对需要返修的缺陷应当分析产生原因,提出改进措施,编制焊接返修工艺(应考虑加工装防焊接变形)后才能开始返修(下表为一般情况下焊缝缺陷及原因分析);
2.焊缝同一部位返修次数不宜超过2次。
3.一般用金属磨头清除缺陷和开坡口。如果缺陷较深时,可先用规定的手工铣打磨,再用金属磨头打磨坡口表面。坡口应宽度均匀、表面平滑和便于施焊的凹槽,凹槽两端有一定的坡度(一般不大于1:4)。
4.返修前需将缺陷清除干净,一般应进行100%PT确认(若缺陷是裂纹,则必须进行100%PT)。补焊时只需将缺陷除尽即可,不要挖得太深,必要时进行RT进行确认缺陷已完全清除。补焊时先不填丝,用电弧对补焊区金属熔化;填丝后电弧应稍偏向焊丝,防补焊区金属过热,电弧可在补焊长度方向上适度往复移动,以延长熔池存在时间,以利于氢气泡从熔池逸出。
5.返修焊缝性能和质量要求应与原焊缝相同;
6.铝焊接主要焊缝缺陷是气孔和裂纹:
6.1 气孔产生原因:铝焊接气孔主要是氢进入焊接熔池而形成的。氢来源有:材料、焊丝、保护气体、送丝机构、焊工的手套和环境湿度太高等,如焊丝被污染、材料及焊丝本身的氧化膜、送丝机构上有油污或汗渍等。预防措施:
6.1.1材料及焊丝内的含氢量≤0.4mL /100g;
6.1.2 被焊件表面应去除油污及氧化膜,存放时间不超过4h。表面清理后应用干燥、洁净、不起毛的物件覆盖坡口及两侧;
6.1.3 焊丝尽量使用抛光焊丝,不然处理方法同上;
6.1.4 保护气体内杂质含量:H2≤0.001%;O2≤0.02%;N2≤0.1%;H2O≤0.02%;
6.1.5保护气体管路:一般采用不锈钢管或铜管,软管采用塑料管而不能用橡胶等易吸水的软管;焊前应检查冷却水管道,确保不会漏水;当环境湿度很大时,应对保护气体进行加热对管路进行吹扫;
6.1.6 送丝机构:不得有油污,送丝管采用聚四氟乙烯管或尼龙,并焊前清理管内污染和冷凝水;
6.1.7现场环境:温度不宜超过25℃,相对湿度不超过50%,保持环境清洁;
6.1.8焊工:工作服装尽量是白色的,以便能及时发现和清理污染。焊时注意汗水和油渍不要再次污染焊件;
6.1.9 在焊前都应在试板上试焊,以便检查保护气体和管路是否合格。
6.1.10 焊接工艺上预防措施:用双面焊代替单面焊;每道焊缝薄时比厚时有利于气孔逸出;大直径焊丝有利于减少气孔;焊前预热、焊后缓冷;降低电弧电压、增大电流、降低焊接速度,有利于减少气孔。
6.2 裂纹产生原因:材料焊接性较差;选择焊丝时没考虑抗裂性;结构的拘束度过大。预防措施:
6.2.1 对焊接性较差的铝材在焊接前应考虑其抗裂性而不能只考虑强度;必要时可考虑对焊件进行退火后焊接,焊后再淬火时效。
6.2.2 选择抗裂纹性好的焊丝,如含Si等低熔点元素的焊丝。
6.2.3 尽量减少焊接接头的拘束度,合理安排焊接顺序,让焊缝能够有横向收缩余量,以减小焊接应力。没有必要定位焊的就不要焊定位焊,能双面定位焊的就不要单面定位焊。
6.2.4 尽量改单面焊为双面焊。
六、探伤要求:
1.封头拼缝焊后应进行100%RT,成形后再按规定100%RT或100%PT。
2.A、B类焊缝一般进行100%RT。
3.容器上的C、D类焊接接头进行100%PT。
4.铝材表面补焊焊缝进行100%PT。
5.铝卡具和拉筋的临时固定连接焊缝拆除后的焊痕等进行100%PT。
6.其他图样要求探伤的部位。
该文章转自于:焊接工艺 https://mp.weixin.qq.com/s/7w_nJX9qnAFywjx5btkNeQ
上一篇:机械零件图纸
下一篇:合金元素在钢中的作用