
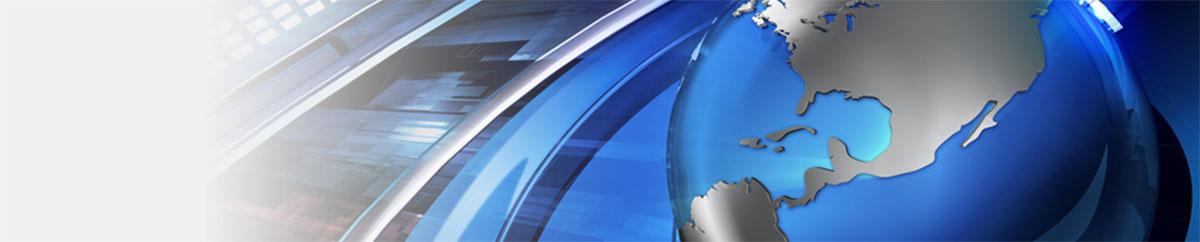
热门文章
变速箱齿轮轴的数控车削
齿轮轴一般加工工序为锻造→正火→粗车→精车→滚齿→滚花键→钻孔→热处理→磨削外圆/内孔→磨齿/珩齿→检查→清洗→包装。个别工序依照图样要求的情况进行改动或调整。通过上序几道工序可以看出工序复杂,加工单元较多。每一道工序当中还可能存在着多道小的工序,可想而知环节较长,保证精度难度较大。
而由于变速箱需求量大,产能高的本身市场特点。全部依靠人工进行操作势必会成为“人海战术”,这对企业运营成本又是很大的负担。为了解决以上两种情况,在保证每道大工序加工的情况下,尽可能缩短小工序和利用自动化组线减少人力使用情况。由于篇幅有限,本文仅对精车工序进行描述。如图1所示,该零件阶梯轴的外圆对两顶尖通轴度要求一致。
1.方法一
一般方式加工往往采用三序,第一序及第二序采用标准液压卡盘及顶尖一夹一顶方式进行两端半精车,第三序采用两顶夹顶紧方式进行精车。
分析:因毛坯料不圆整,夹持外圆同时又受尾台顶尖力情况会造成轴沿圆周方向和轴向有串动趋势,又因加紧定位为刚性形式,故在加工中轴线会产生弯曲现象(见图2,没有后拉和补偿的卡盘,卡爪翘起,把轴推离中心定位,尾座的力必须克服这个翘起的力,否则将会导致工件的弯曲)。造成零件动刚性不足,加工中也容易发生零件振动。另外也因毛坯外圆不圆整问题,齿轮轴同一端头处必须进行至少二次加工找正将夹紧端外圆进行修正。因二次装夹会造成两端头不同心现象,在第三序进行精加工时需要一定的留量再进行半精车来保证最后一道精加工余量均匀。
此种加工方式夹具简单,设备的成本较低,但工序较多多次装夹精度相对难以保证一致,使用人工也较多,总体加工节拍太长,机床数量增加,占地面积较大。
2.方法二
在方法一的基础上改用第一序采用顶尖浮动卡爪卡盘夹紧,尾台顶尖顶紧齿轮轴,第二序采用顶尖后拉卡盘夹紧(见图3),尾台顶尖顶紧齿轮轴,第三序采用两顶夹顶紧方式进行精车(见图4,尾座只提供支撑零件所必须的力,卡盘把工件拉向中心顶尖,工件不发生弯曲,加工出来的轴的圆柱度和同心度非常好)。
分析:第一序改用顶尖浮动卡爪卡盘夹紧后,因卡爪为浮动机构,本身不起到定心作用,同时在传递圆周方向上的扭矩有所增大。两端同心情况要好于方法一。
第二序采用定价后拉卡盘,后拉卡爪向卡盘方向用力,使得轴线有弯曲趋势的齿轮轴有所“伸长”,起到预拉伸作用。零件动刚性有所提高。
第三序加工时,因前两序的加工,故此序留量比较均匀,加工余量可以减小,可以不再进行半精车校正,必要时可采用一刀完成。
此种方式弥补了零件加工过程中同心较差、加工零件动刚性不足和精加工余量较小的情况。但夹具形式较复杂,夹具成本较高。没有减少设备数量和人工成本,总体加工节拍也基本不变。
3.方法三
在方法二的基础上再次进行改进,改用端面驱动复合卡盘配合尾台顶尖进行加工(见图5)。该夹具卡爪仍采用浮动机构,顶尖端部增加顶压式小卡爪(小卡爪直径小于所加工齿轮轴的直径)。当毛坯进行上料时,浮动爪(大卡爪)伸出夹持外圆,尾台顶紧后进行加工(见图6)。当加工完毕后,浮动卡爪沿轴向收回,顶尖处的小卡爪伸出辅助两顶尖轴向顶紧齿轮轴(见图7)。卡爪轴向高度小于夹紧端端面,给卡盘处留有刀杆加工位置,进行剩余未加工的部分。
此种加工方式运用一次装夹即可完成齿轮轴的外圆加工。减少了装夹时间及加工节拍、设备数量及场地面积、人工数量等。此夹具结构复杂,夹具成本较高。但以上资源节省后,总体比较是非常划算的。
4.结语
目前市场上最为普遍的齿轮轴加工方式大多采用第一种,随着运营成本的不断提高,采用新型的加工方式也渐渐收到关注。通过以上三种加工方式的比较,第三种是比较划算的。当然客户可依照自身情况进行适当选择。
该文章转自于:机工刀具世界 https://mp.weixin.qq.com/s/Avvn9Q0Bx4hjMiChvs-Sqg
上一篇:汽车发动机缸盖加工刀具的选择
下一篇:合金元素在钢中的作用